The ASHVIN project develops a set of digital twinning alternatives targeting the European construction sector and civil infrastructures. These alternatives allow connecting IoT-enabled digital twin platforms to different digital twin tools with validated and standardized procedures. The ASHVIN solution aligns with the major goals of the European building Industry of improving building efficiency while reducing costs and increasing operational intelligence. The developed systems are inspired, grounded, piloted and applied in 10 European demonstration sites. One of these is demonstration site #9 Olympiastadion of Munich. Two ASHVIN partners, sbp (Burkard Krenn) and UPC (Rolando Chacon & Carlos Ramonell) lead the implementation of the feasible solution according to the site conditions. The analysed structure is a specific sector of the roof of Olympiastadion. Presently, maintenance activities in Olympiastadion are managed by Stadtwerke München (SWM) who granted access to ASHVIN partners to the premises of the sector under twinning.
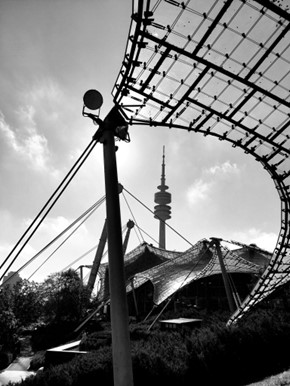
Olympiastadion. Das Halle and Olympiaturm
What is demo site # 9?
Olympiastadion in Munich was built for the 1972 Olympic Games, and therefore it recently celebrated its 50th anniversary. This impressive cable net structure is, from an aesthetic-architectural point of view and as a technical venture, an icon of the construction and engineering art of the second half of the 20th century. The Olympiapark Ensemble is one of the most important event venues and sports centres in the south of Germany.
The Olympic tent roof structure consists of four almost independent and highly prestressed cable net constructions. In total, the cable net forms a roof area of 74,000m2. Before the 50th anniversary, a comprehensive structural survey was carried out by sbp and Prof. Feix ingenieure (Munich). As part of this investigation, a complete static model of the cable net construction was done for the first time since the roof’s existence. The core task was to determine the existing internal force or pre-stressing state in the cable net structure using novel calculation techniques in combination with cable force measurements.
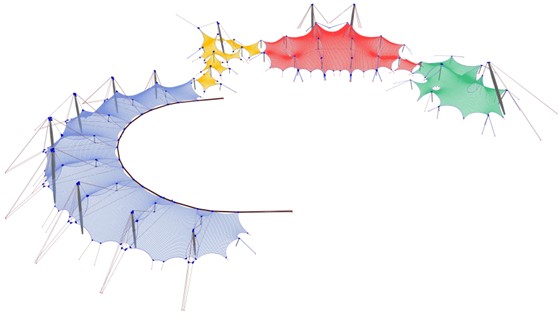
Virtual model developed at schlaich bergermann partner (sbp)©
Measuring the real internal forces in such a structure without a major intervention is unfeasible. Deploying a major intervention in such a complex structure is not an option. One big question arises. Can one measure these forces without the need of a major intervention? This conundrum is approached using remote sensing and reverse engineering. Can one understand changes in the distribution of the forces by measuring the movements of the nodes of the cable net? Answering this conundrum under certain conditions shaped the way this particularly demo site twinning was approached by ASHVIN partners.
How ASHVIN runs on the demo site?
Generating a structurally meaningful Digital Twin of such a complex asset represents a major challenge. To determine the cable forces, only remote sensing methods were considered. Stringent conditions at the site suggested the use of laser scanning only. Neither UAS nor physical access to the roof was permitted. Initial guesses suggested that comparing measurements taken at different seasons, times and temperatures could give hints on the global behaviour of the asset. To understand better the procedure, a mock-up test was developed at the Laboratory of Digital Models in Structures and Construction at UPC. The Force Density Method (FDM) was used for the design of the net. It was implemented using a Python script within Rhinoceros-Grasshopper framework. A terrestrial laser scanner (TLS) was used for the sake of acquiring information related to the structural state of the asset, implementing systematic data-gathering assessments with a systematic variation of actions (in the elastic domain) for establishing the information pipeline. Thus, Information pipelines from measurement to models to BIM were first tested at a laboratory scale.
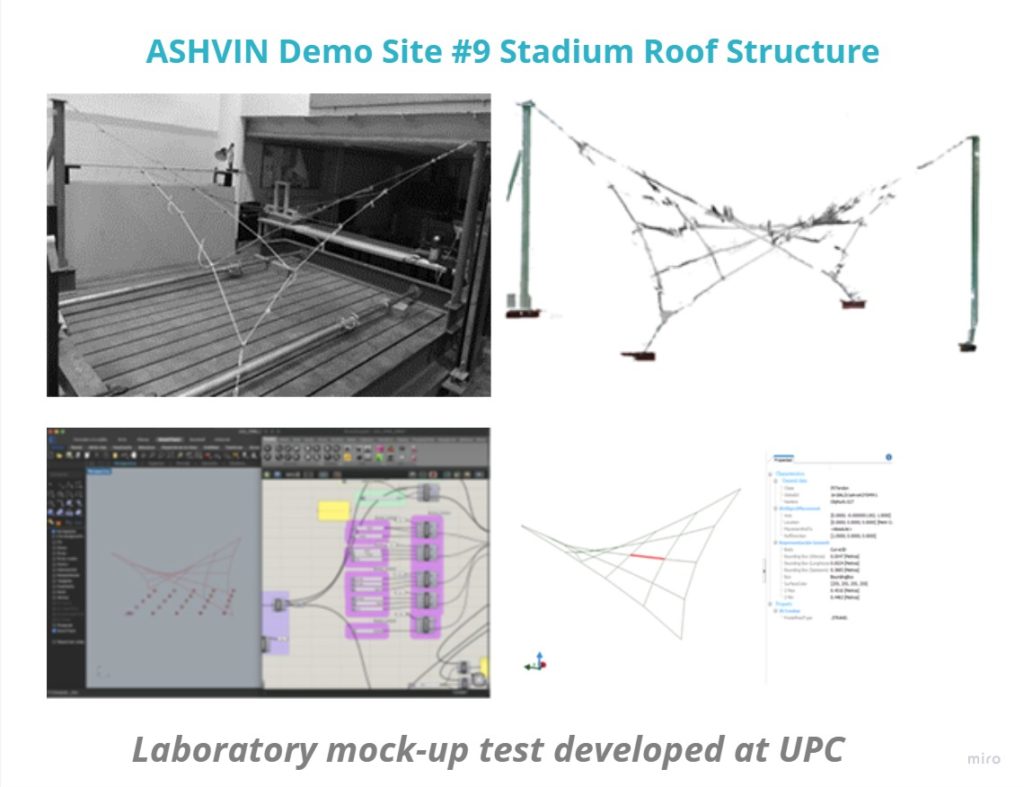
What is the status?
Data collection is in progress – the first three sets of measurements have been carried out in June, November 2022 and February 2023. Measuring the position of the nodes with point clouds in different seasons is under analysis. Displacements and the effect of temperature on the cable net is presently under scrutiny. For developing efficient and systematic segmentation and identification of specific elements of the cable net (nodes, cables, masts), CERTH, an ASHVIN partner is developing tailor-made algorithms. Once identified systematically, the structural analysis of the roof is performed with enabling ASHVIN tools (MatchFEM), developed at UPC, as well as with structural analysis components used by sbp in recent years.
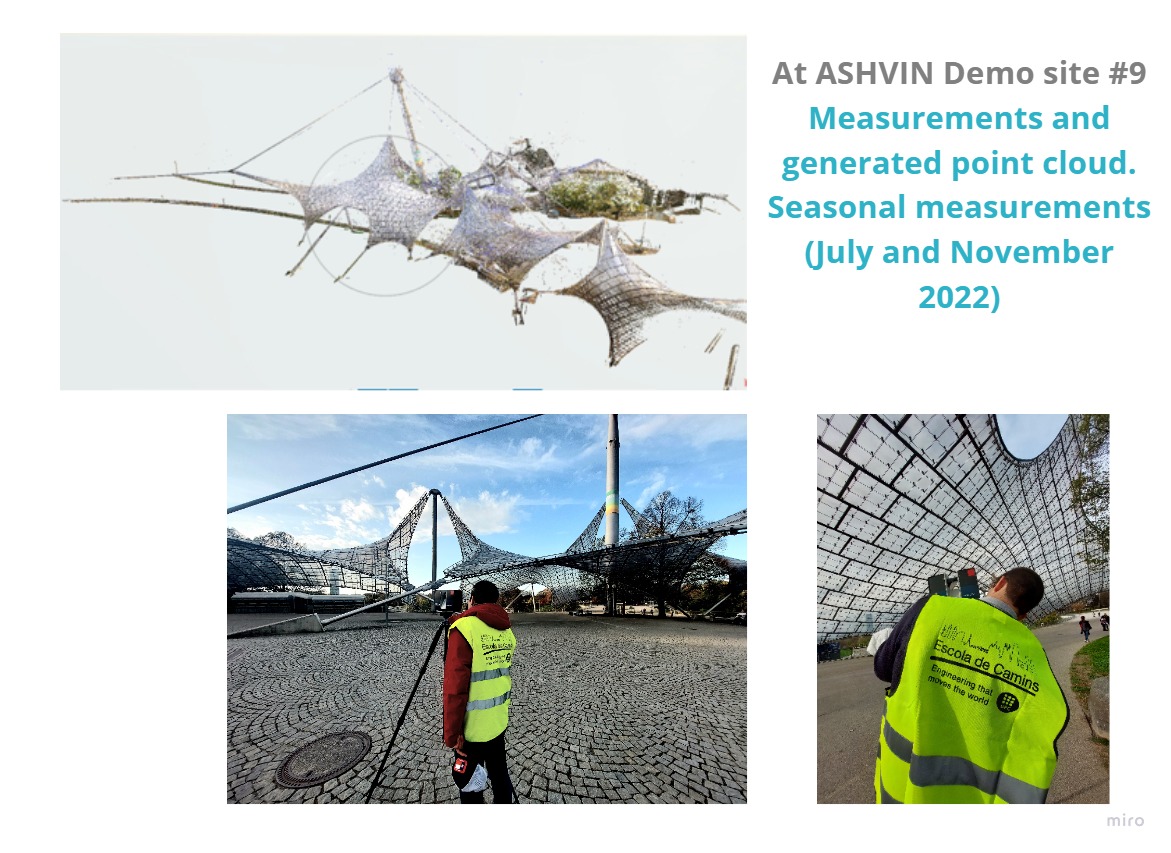
What challenges have been faced?
Both physical and digital challenges have been encountered. For the former, stringent conditions established by managers such as no UAS, no physical access to the roof, and no installation of reflectometers, accelerometers or gauges shaped the approach to measuring. Remote sensing techniques were thus tried as an option. It is worth noting that this method can be considerably cost-efficient for managers as a SHM technique of the asset.
For the latter, point clouds of the targeted sector (orange sector in Fig. 2) resulted in extremely large files. Systematic identification of useful elements (nodes and cables) has resulted in a complex mathematical challenge. Solving this challenge is one of the ASHVIN contributions to the demosite.
What are the next steps?
The final set of data measurements will be conducted in the summer 2023, which will have given a complete cycle of seasons during a whole year. This may result in the generation of the first living digital twin model of the stadium roof structure, which may represent a cost-effective methodology that may help support the asset managers in understanding the behaviour of the roof with no major intervention.
What is the desired impact?
As one of the demonstration sites, the goal is to develop a digital representation and correlate data of measurements with the structural model. The aim is to improve future maintenance and asset management, and access measurements with minimal intervention.
We thank SWM for the access and for the permission to carry out the measurements!
For more information, visit our Digital Toolkit Page, and connect with us through our LinkedIn or Twitter communities!